..Now remember, I wanted to lean the neck back one degree or so. Let's consider the math for that. Imagine (or just look at the following diagram) the banjo laid on a table, strings down, body to the left, head toward the right. It's resting on the bridge and the body is perfectly horizontal. The neck is angled up a degree or so... we want to know exactly how much of an angle to angle it.

(Wow, this blog software aches. If anyone thinks Google is really competent, just click on the above image to see it as I created it...)
The cookie tin has a rim around the edge that sticks "up" (down, in this diagram) and we want to postition the neck so it's flush with this, or pretty close.
Now, notice that while the neck angle n and the string angle s are almost the same, they are not exactly the same. The situation is like this:
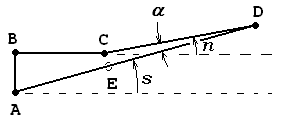
The line AD is the strings; CD is the neck. The strings' clearance CE at the rim should be about 5-6 mm but at the grin D it should only be about 2 mm. Therefore the two angles are a little different. (The strings vibrate within an envelope that is wider in the middle than at the ends.) The difference between angles s and n is the angle
alpha, which we'll call the action angle.
I have neglected the height of the grin but this wont matter much. You can figure it in, if desired.
BC is a line, not exactly the face of the tin but a horizontal line floating "above" the face, at the height of the rim.
Let's write down some measured or likely dimensions:
bridge height: 13 mm
rim height: 3 mm
neck length, chin to rim: 470 mm
bridge to rim: 150 mm
So the length of line AB is the bridge height minus the rim height, or 13 - 3 = 10 mm. The distance A-E is about 150 mm. It's not that exactly but we can approximate it so, since the radius and the cosine are pretty close to the same at small angles like this. The height of point E above the table is then 150 sin(s) or just 150 s, since the sine and tangent functions are also pretty close to the angle in radians. The clearance CE is this height subtracted from the length of AB, or 10 - 150s. Now the action angle
alpha can be calculated from the clearance CE and the neck length CD; in radians it's just CE / CD, or approximately so. Then the neck angle n is just the string angle minus the action angle, s -
alpha.
Let's use a spreadsheet to map out the territory. First, generate down the left column a series of string angles from say, 1 to 3 degrees. Then in the second column convert these to radians. In the 3rd column, calculate the clearance by the above formula. 4th column, calculate the action angle, and 5th column, the neck angle. The last column just converts the neck angle back to degrees.

So to get a clearance of 5 to 6 mm, we should set the neck angle to be about 1 degree.(yellow area.) Somehow I guessed that correctly; probably just from looking at some banjos in the store.
If this gets us anywhere near, we can fine-tune it via bridge height if desired.
Of course this all depends on the exact geometry of your banjo. YBMV
As a sanity check, if we run this spreadsheet out a bit, the string angle and the neck angle will be exactly the same at the point where the clearance goes to zero. And this is so:

_____________________